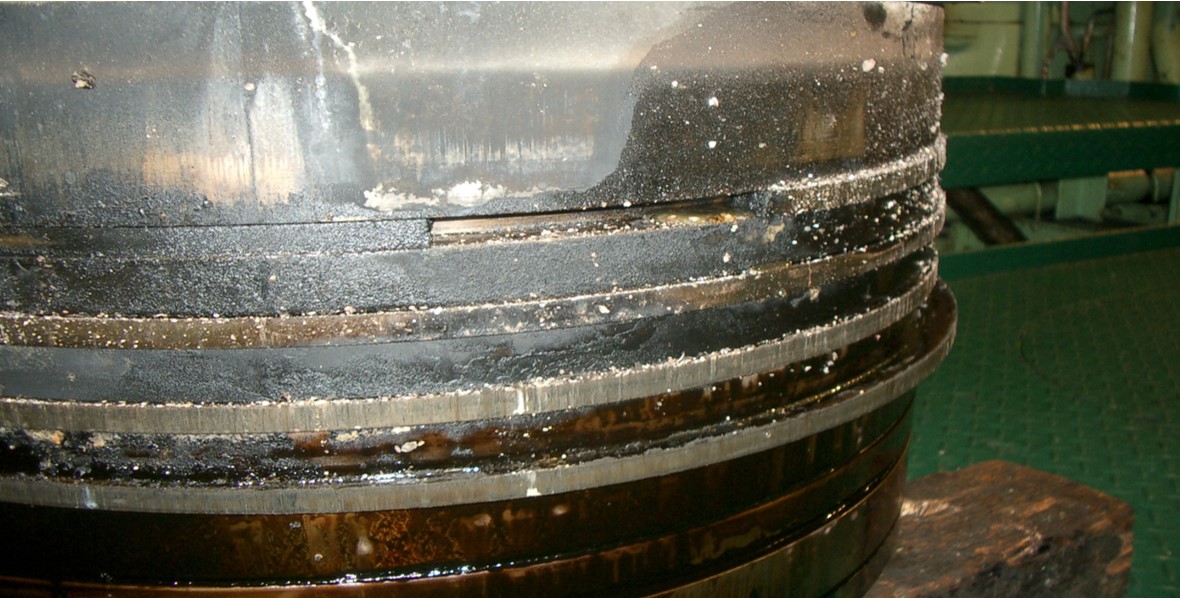
INTRODUCTION TO
Cylinder wear in two-stroke engines
Efficient cylinder lubrication does not eliminate the wear of liners and piston rings completely. The goal is to control the cylinder wear rate and keep it on a normal level and to prevent other harmful types of wear.
Cylinder wear in two-stroke marine engines refers to the gradual deterioration of the inner surface of the cylinder where the piston moves. This wear can occur due to various factors including friction between the piston rings and cylinder walls, abrasive contaminants in the fuel or lubricating oil, inadequate lubrication, and high temperatures. Over time, this wear can lead to increased clearance between the piston and cylinder, reduced compression, decreased engine performance, and potentially even engine failure if left unaddressed.
The wear of large engines running components is generally attributable to either abrasive wear or adhesive wear. The main causes of cylinder wear in two-stroke diesel engines can be:
- Improper running- in of a new engine
- Inadequate lube oil supply causing surface contact
- Lube oil has too low viscosity or too low in alkalinity (BN number)
- Contamination of lube oil by abrasive material
- Inefficient combustion such as carbon deposits
- Adhesive friction from rubbing between piston rings and cylinder wall
- Abrasive Contaminants: Presence of abrasive particles in fuel or lubricating oil
- Improper Maintenance: Neglecting regular maintenance tasks
Abrasive wear
Abrasive wear is a type of mechanical wear caused by the relative motion between two surfaces in contact, where hard particles or abrasive contaminants between the surfaces cause material removal.
It occurs when a hard rough surface slides across a softer surface; in this case, wear is defined as a damage to a solid surface that generally involves progressive loss of material and is due to relative motion. Abrasive wear on cylinder liners and piston rings manifests as rough, scratched surfaces. This roughness poses a significant issue by increasing the formation of the hydrodynamic oil film essential for lubrication.
As the oil seeps into the scratches, the peaks of these imperfections on both the cylinder liner and piston ring surfaces come into direct contact, leading to metal-to-metal contact. This exacerbates wear and heightens the risk of further damage if left unattended.
Piston ring wear
A type of abrasive wear specifically affects the piston rings. To ensure optimal engine efficiency, it’s essential to keep the piston clear of deposits, allowing the rings to move freely. This freedom of movement is vital as the rings play a key role in sealing the combustion space tightly.
Accumulation of deposits like combustion residue, wear particles, and unused lubrication oil can lead to piston ring sticking. This can cause excessive load during operation, ultimately resulting in ring breakage.
The build-up of light deposits around the piston rings must be addressed to avoid blow-by and accelerated wear. It is typically not a problem having deposits on top-land, if the piston clearance ring (or anti-polishing ring) is in good order.
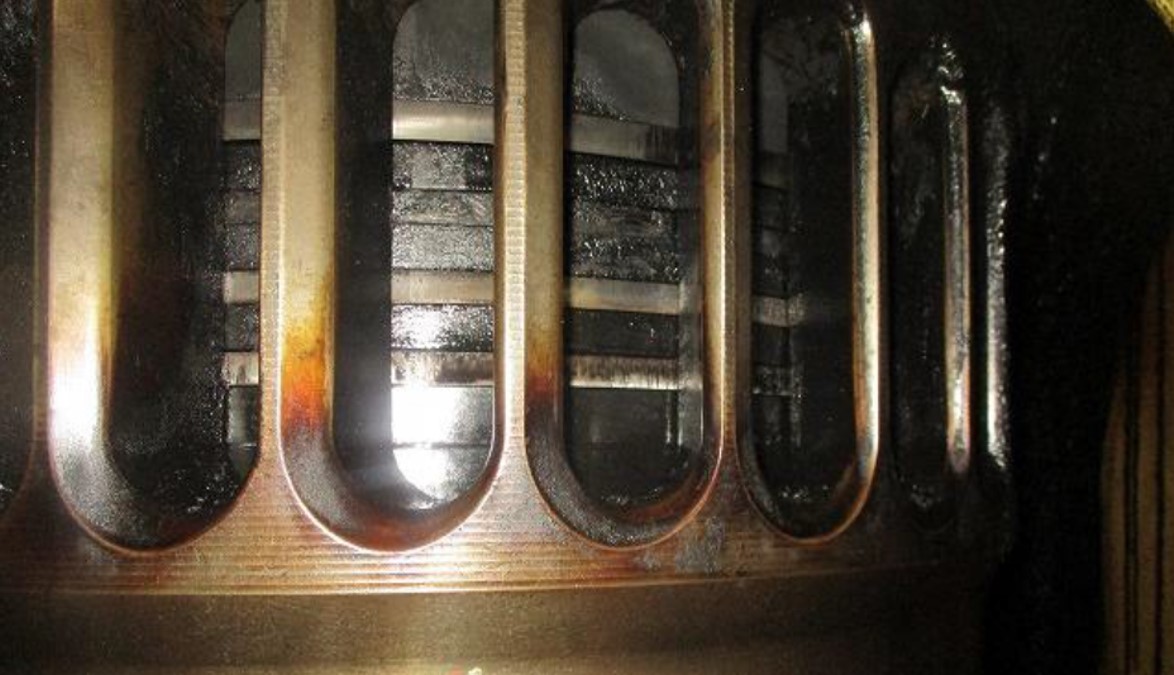
Close-up: deposit build-up on piston rings
Blow-by
Blow-by refers to the passage of combustion gases past the piston rings, leading to decreased efficiency and contamination of crankcase oil. Additionally, leaked combustion gases can enter scavenge spaces, causing fouling and potentially resulting in scavenge fires. This issue often stems from broken piston rings or rings becoming stuck due to excessive lubrication or the use of improper lube oil.
Adhesive wear
Adhesive wear occurs when the oil film oil film between piston ring and liner is lost, causing metal-to-metal contact. This increases friction and temperature, potentially leading to localized bonding known as micro-welding. Consequently, surface scuffing or macro-seizures, may occur. When micro-welding, or micro-seizures, occur, the surfaces become roughened and may continue to breach the oil film during contact. In response, it is a common practice to increase the lube oil feed rate, reducing pressure between the mating surfaces and thereby alleviating engine load.
If left untreated, the wear can escalate into macro-seizures, resulting in temporary high wear of the mating parts. If scuffing occurs in the combustion chamber between piston ring and liner, it is necessary to replace or machine the components to eliminate the damaged layers.
Liner scuffing wear
Scuffing occurs when lubricated surfaces experience adhesive wear due to the breakdown or failure of the lubricant film. It involves micro- welding” between cylinder liner and the piston rings due to metallic contact. Scuffing can be caused by a variety of factors, either individually or in combination.
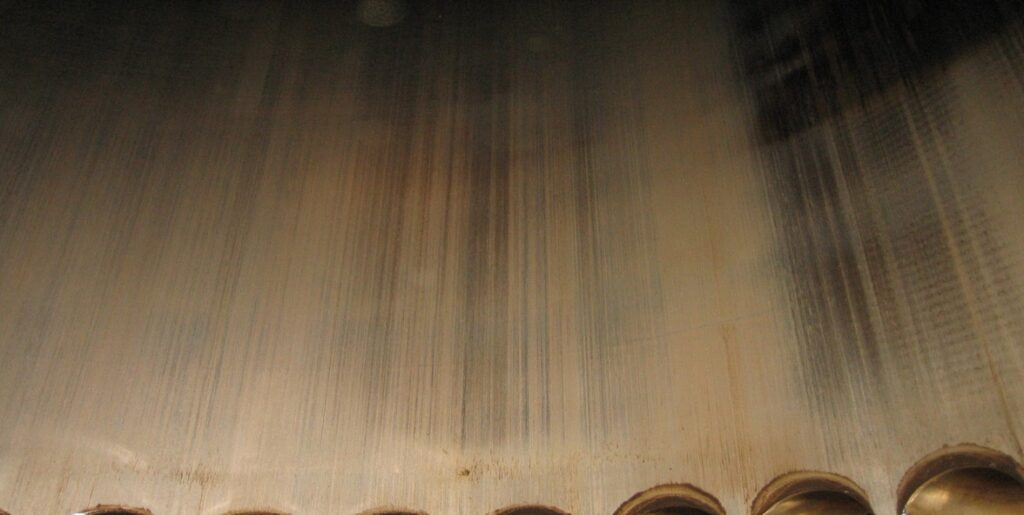
Cylinder liner exposed to scuffing
Scuffing starts when the oil film between the piston ring running surfaces and the liner wall breaks down, leading to adhesion, or micro welds. As these micro welds multiply it can cause surfaces tearing, dragging, or furrowing of one or both surfaces until they break apart. In the long term, scuffing can become a costly issue for ship owners, resulting in lost operating hours and increased demand for spare parts.
Green fuels
The emergence of new dual-fuel engines utilizing eco-friendly fuels like Methanol or Ammonia is not expected to introduce significant new problems or unfamiliar types of wear. Our preliminary analysis suggests that the future of marine engine operation will emphasize deposit control and cleaning as key priorities.
One reason for concern is the intermittent lubrication approach employed by OEM lubrication systems in marine engines. This method involves injecting lube oil once, followed by several piston strokes before the next injection. Therefore, there may be a tendency to over-lubricate to compensate for these ‘dry strokes’.
This can lead to the accumulation of excessive calcium deposits around the piston rings, resulting in reduced ring movement and flexibility, with scuffing being a potential outcome.
Another challenge is emulsification between the lube oil and the fuel in use. Standard lubrication systems use the lube oil over longer time intervals between lube oil injections allowing emulsification that reduces viscosity of the oil. Thereby lubricity is reduced which may break the oil film and cause scuffing where the piston rings get in direct contact with the liner surface.
Flexible lubrication leads the way
The primary objective of cylinder lubrication in marine engines is to minimize friction between piston rings and the liner, thereby improving engine efficiency. Effective distribution of the lubricant inside the cylinder is crucial for neutralizing acids formed during combustion. Moreover, employing flexible lubrication algorithms assists in cleansing the cylinder of deposits and ensuring a gas-tight seal, further enhancing engine performance.
In today’s maritime industry, efficient cylinder lubrication is more critical than ever. With the increasing complexity of engines, the adoption of dual fuels, diverse operational patterns, and evolving environmental regulations, the importance of effective lubrication systems has reached new heights. These factors collectively shape the path towards a greener future for maritime operations, emphasizing the pivotal role of cylinder lubrication in this transition.
Efficient lubrication plays a crucial role in enhancing vessel productivity, reducing operational cost, and minimizing emissions in the maritime industry. Hans Jensen Lubricators offers cutting-edge solutions designed to address various to address various challenges, safeguarding vessel engines and maintaining productivity in the dynamic maritime environment.
Are you struggeling with cylinder wear?
-then talk to our engineers.
Fill out the form and a representative will get back to you shortly.